Porosity in Welding: Identifying Common Issues and Implementing Best Practices for Avoidance
Porosity in welding is a prevalent concern that frequently goes undetected up until it causes substantial problems with the stability of welds. In this discussion, we will certainly explore the vital variables contributing to porosity formation, analyze its harmful results on weld efficiency, and discuss the finest methods that can be adopted to decrease porosity occurrence in welding processes.
Usual Reasons For Porosity
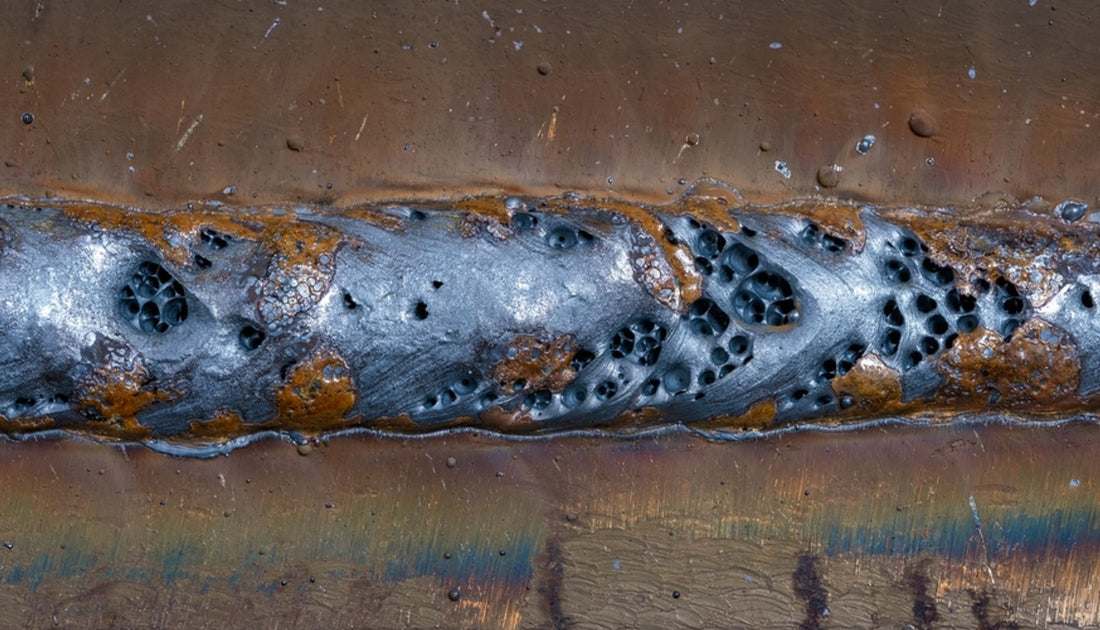
Another regular wrongdoer behind porosity is the presence of pollutants on the surface of the base metal, such as oil, oil, or rust. When these impurities are not properly eliminated before welding, they can evaporate and come to be entraped in the weld, triggering issues. Furthermore, making use of dirty or wet filler products can introduce pollutants right into the weld, adding to porosity issues. To minimize these usual root causes of porosity, thorough cleansing of base steels, proper shielding gas selection, and adherence to optimal welding specifications are vital practices in accomplishing premium, porosity-free welds.
Effect of Porosity on Weld Top Quality

The existence of porosity in welding can substantially jeopardize the architectural integrity and mechanical properties of welded joints. Porosity creates voids within the weld steel, damaging its total toughness and load-bearing capability.
Welds with high porosity degrees have a tendency to display lower effect toughness and decreased capacity to deform plastically prior to fracturing. Porosity can impede the weld's capacity to efficiently transfer pressures, leading to premature weld failure and potential security threats in essential frameworks.
Best Practices for Porosity Prevention
To boost the structural integrity and quality of bonded joints, what specific actions can be executed to decrease the event of porosity throughout the welding process? Porosity avoidance in welding is essential to make sure the honesty and strength of the last weld. One efficient practice is appropriate cleaning of the base metal, getting rid of any contaminants such as corrosion, oil, paint, or dampness that could cause gas entrapment. Making sure that the welding tools is in good condition, with tidy consumables and appropriate gas flow rates, can additionally dramatically lower porosity. In addition, keeping a steady arc and controlling the welding criteria, such as voltage, existing, and travel rate, helps develop a consistent weld pool that reduces the risk of gas entrapment. Making use of the right welding strategy for the details material being welded, such as adjusting the welding angle and weapon position, can even more protect against porosity. Normal inspection of welds and prompt remediation of any kind of problems determined during the welding procedure are crucial practices to avoid porosity and generate top quality welds.
Value of Proper Welding Techniques
Carrying out appropriate welding strategies is extremely important in making certain the structural integrity and high quality of welded joints, building on the structure of effective porosity avoidance measures. Welding strategies straight influence the overall strength and longevity of the welded framework. One key element of correct welding methods is maintaining the right heat input. Too much warm can bring about increased porosity due to the entrapment of gases in the weld swimming dig this pool. Conversely, not enough heat might result in insufficient blend, developing possible powerlessness in the joint. Additionally, utilizing the proper welding criteria, such as voltage, present, and take a trip rate, is critical for achieving audio welds with very little porosity.
In addition, the choice of welding process, whether it be MIG, TIG, or stick welding, must straighten with the specific demands of the task to guarantee ideal results. Proper cleaning and prep work of the base steel, in addition to choosing the ideal filler material, are also necessary parts of competent welding strategies. By sticking to these finest practices, welders can reduce the danger of porosity formation and generate high-grade, structurally audio welds.
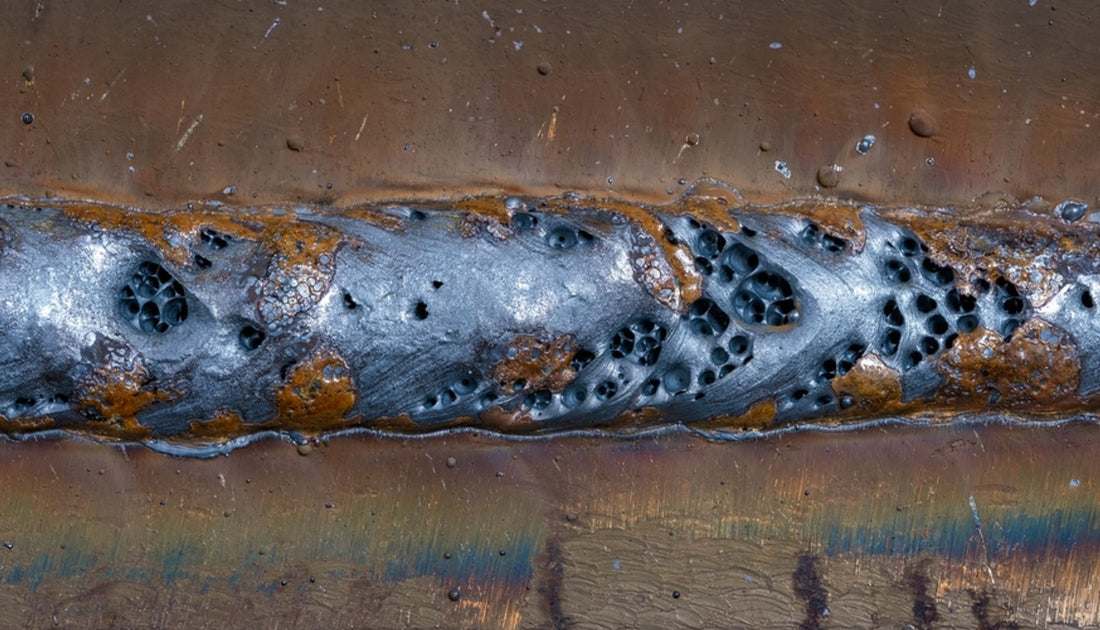
Examining and Quality Assurance Measures
Testing treatments are crucial to discover and protect against porosity in welding, guaranteeing the toughness and toughness of the final item. Non-destructive screening methods such as ultrasonic testing, radiographic screening, and visual evaluation are typically utilized to recognize prospective issues like porosity.
Post-weld assessments, on the various other hand, assess the last weld for any kind of flaws, consisting of porosity, and confirm that it meets defined requirements. Executing a comprehensive quality control strategy that consists of detailed testing procedures and assessments is paramount to reducing porosity issues and making certain the overall top quality of bonded joints.
Verdict
In verdict, porosity in welding can be a common issue that impacts the high quality of welds. By recognizing the typical sources of porosity and executing ideal practices for avoidance, such as appropriate welding methods and testing steps, welders can make sure top quality and dependable welds. Find Out More It is important to focus on avoidance methods to decrease the go to these guys occurrence of porosity and keep the stability of bonded frameworks.